- Home
- >
- Preservation Archaeology Blog
- >
- Hands-On Archaeology: How to Make Adobe Bricks
(November 4, 2018)—In August, I was invited to participate in an adobe-brick manufacturing workshop hosted by the National Park Service at its Desert Research Learning Center on Tucson’s east side. The instructors were local adobe experts with extensive restoration and stabilization experience.
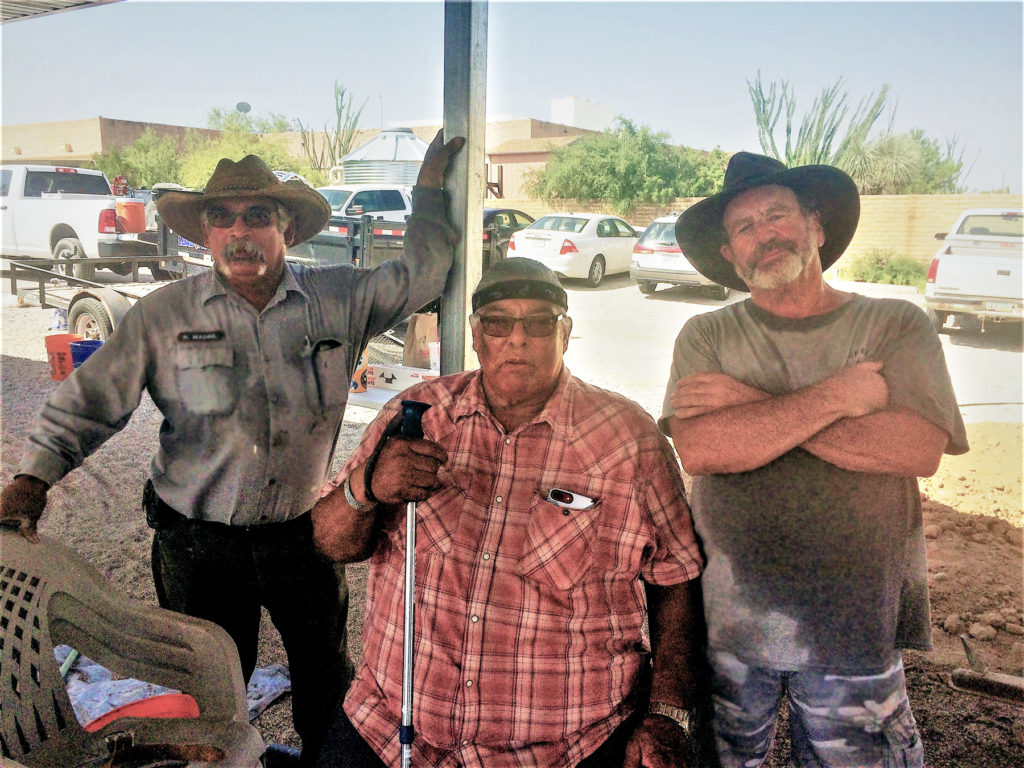
The goal of this workshop was to teach park service employees and interested folks like me how to make the kind of adobe bricks that may be used to repair historic structures suffering from weathering and neglect. Over the course of three days, participants made almost 700 bricks. The bricks will be built into 20 short wall segments that will be used to test weathering on adobe walls and ways to prevent it.
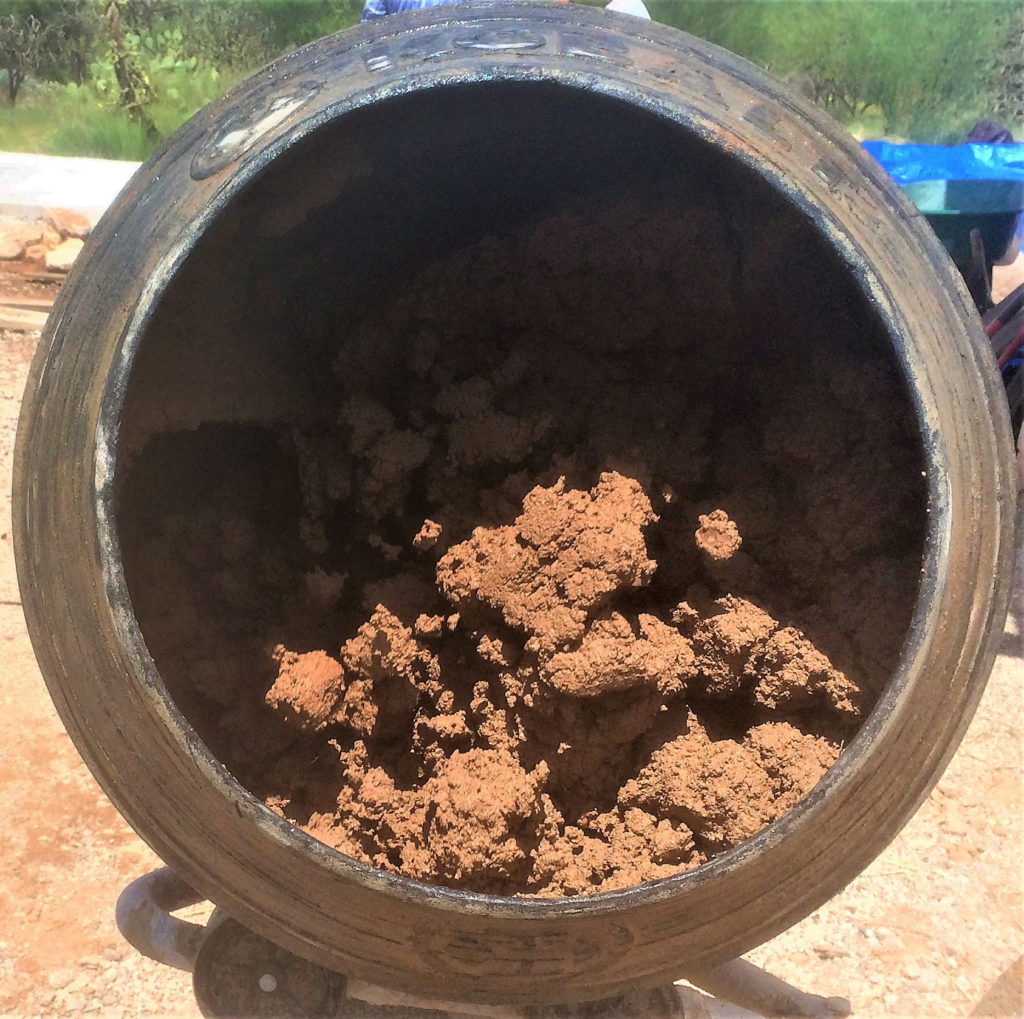
This is a batch of adobe, ready for use. The soil we used was from a local sand-and-gravel company. It had fairly high clay content, so we added sand to keep it from cracking. The best mix for bricks has a lot more sand than what I like for my ancient house replications—I’ve found that when my mix for puddle adobe and wattle-and-daub (jacal) is too sandy, it won’t adhere well.
We used two cement mixers to mix the adobe. We poured the sand and clay into the mixer with 15 gallon buckets. We mixed roughly 1 part soil to 2 parts sand; the formula varied bit from day to day, because different sands had different moisture contents and therefore worked differently. We added water with a hose as the mud and sand were mixed together. When the right mixture was achieved, we poured the adobe into a wheelbarrow and took it to the brick-making area.
![]() |
![]() |
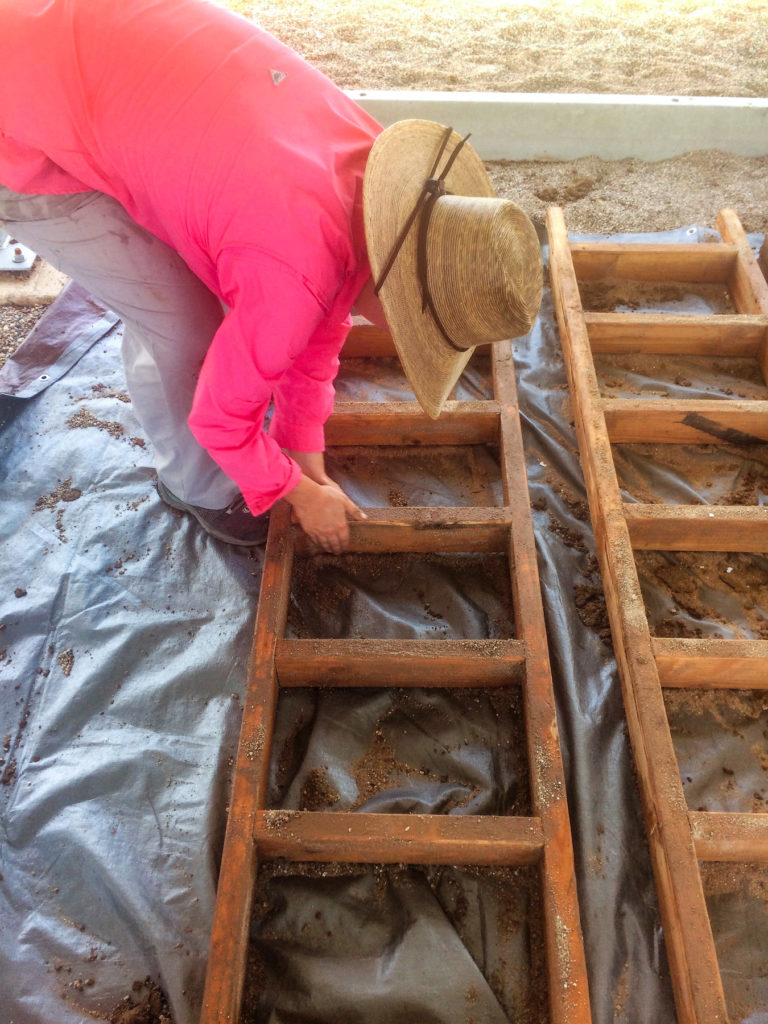
The molds made bricks that were 15 5/8” x 9 5/8”, the typical size for Spanish colonial bricks. We had 6-brick and 2-brick molds made of 2 x 4s. As production progressed, it was clear the 6-brick molds were much more efficient than the 2-brick molds. The molds were washed and coated with sand or soil between uses so the adobe would not stick.
We threw or scooped mud into the molds and compressed it by hand to ensure it was compacted down and filled in the corners nicely. We then smoothed the tops so the bricks would be flat and have a consistent thickness.
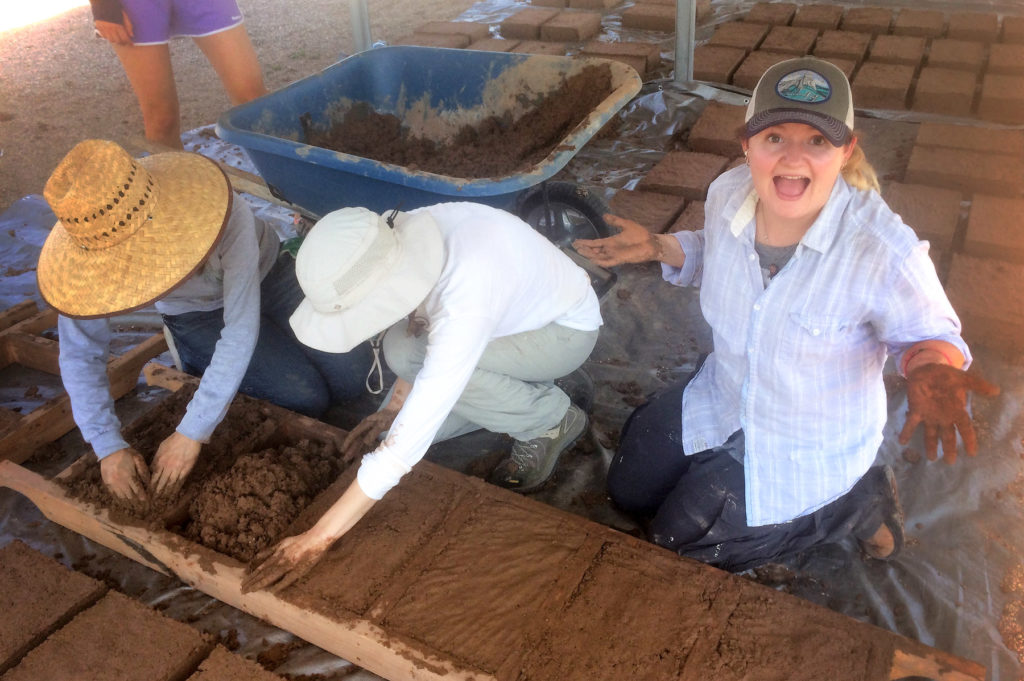
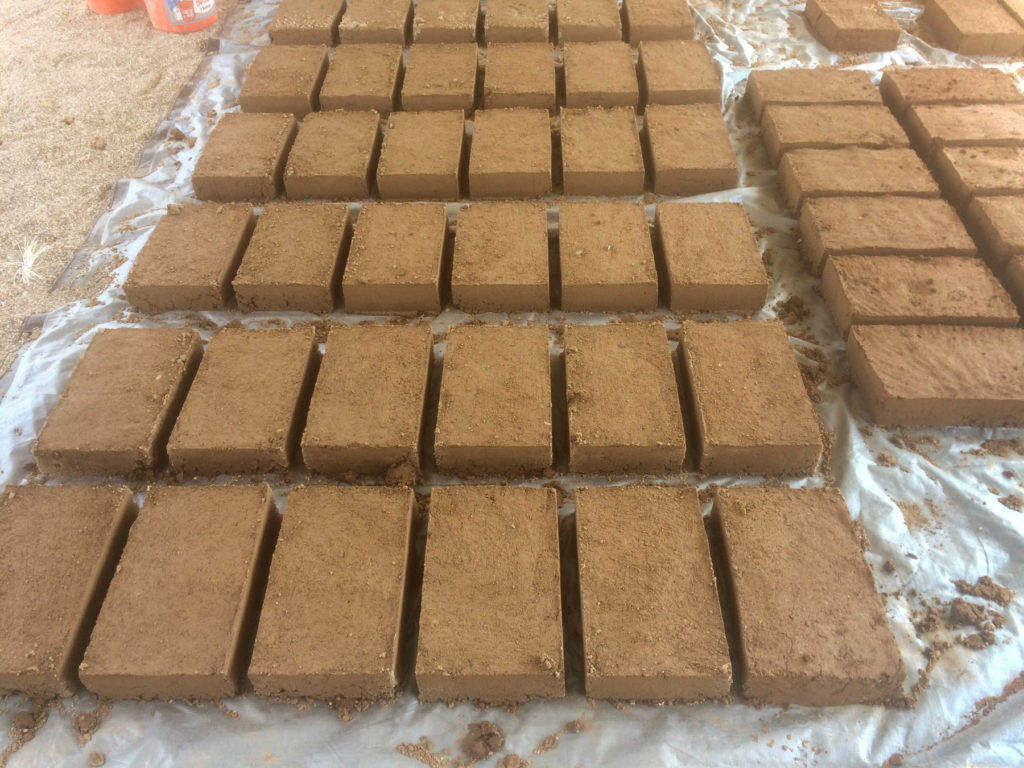
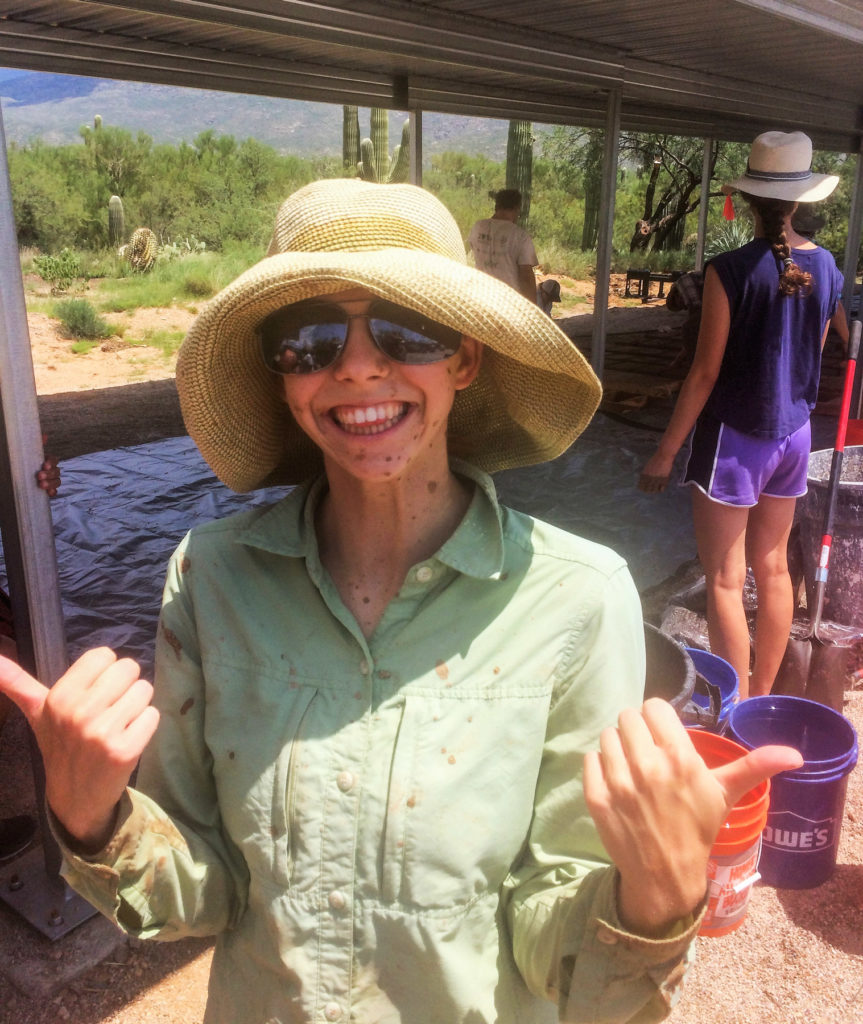
In a couple of weeks we will come back and build the footers for the test walls. I will show this process and wall construction in my next post.
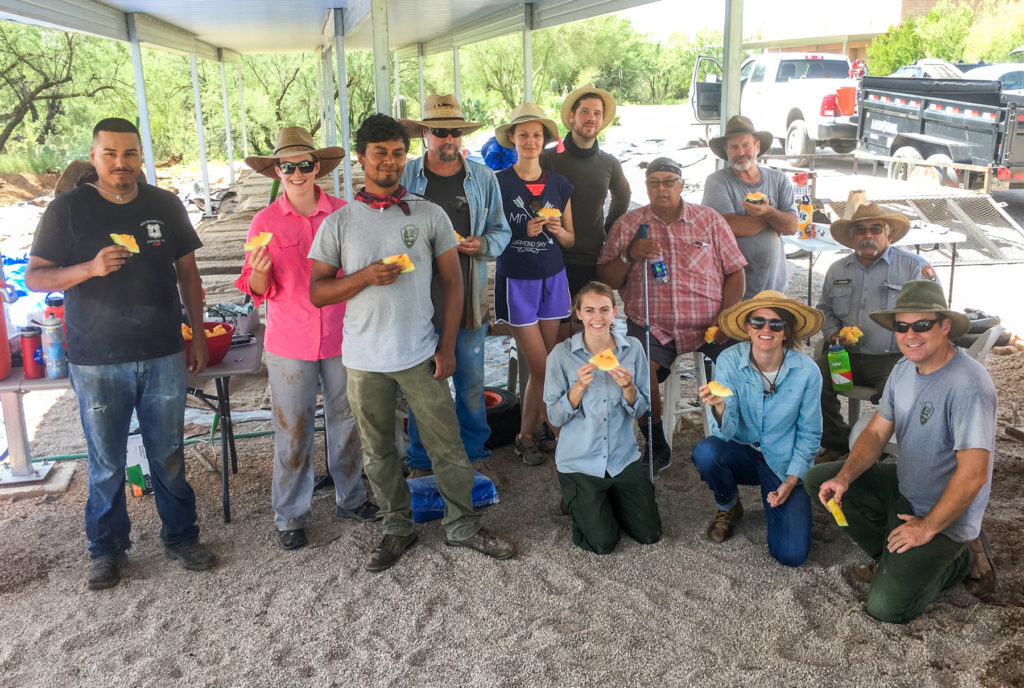